Shotcrete is a special concrete that you can spray onto a surface, with shotcrete application as a ground support system in mining and tunneling sectors. Shotcrete offers benefits over conventional concrete in various construction purposes due to fewer formwork needs, needing only a small portable plant for placement and manufacture.
How Strong is Shotcrete?

The high cement factors, low water-cement ratio, and good shotcrete compaction usually produce strong, dense, and well-bonded materials. To get the maximum strength of the shotcrete, you should take the help of an experienced nozzle-man. The shotcrete has higher compressive strengths than cast-in-place concrete. The compressive strength of the shotcrete is in the range of 6,000-7,500 psi. You can also add the latex modifiers to shotcrete that will provide freeze-thaw durable material.
What is the Shotcrete Process?
There are two types of shotcrete processes, such as:
Dry Mix
In the dry-mix process, the cement mixture and damp sand are conveyed via a delivery hose pipe to a unique machine gun known as delivery equipment.
The mixture is metered into the delivery hose by a feed distributor or wheel; this material is carried by compressed air perforated manifold. Introduce water under pressure and follow by mixing it with other materials.
The mortar flowed from the nozzle at high velocity onto the surface that is shotcrete. In this process, you can accomplish any alteration in the water quantity easily via nozzleman. If the water is more, concrete will be slumped when shot on the vertical surface. You should adjust the water so that the material wastage is rebounding at minimum level. You should also make sure that the water ratio is between 0.33 and 0.50.
Several equipment forms are accessible for shotcrete by this technique. The equipment ensuring a constant supply of the mortar can transport the material to a distance of 300-500mg horizontally and 45-100 m vertically.
Wet Mix Process

You should mix all the ingredients such as cement, sand, water, and small-sized coarse aggregate before filling it in the delivery equipment chamber in this process.
The mixture is later metered into 7 atmospheres to a nozzle; you can inject additional air in the nozzle to get more velocity and enhance the running pattern. The estimated range of rebound ranges from 5-15% for horizontal slabs and 20-50% for covering the overhead corners and surfaces.
Most people prefer the dry mix process for lightweight concrete use because the lower water-cement ratio results in higher strengths, less creep and dry shrinking, and more durability. In comparison, you can get higher durability in the wet mix process with the help of air-entraining agents.
The wet-mix process has various advantages for example it provides less rebound and excretes less dust compared to the dry-mix process. You can also place a large volume of shotcrete in less time.
Conclusion
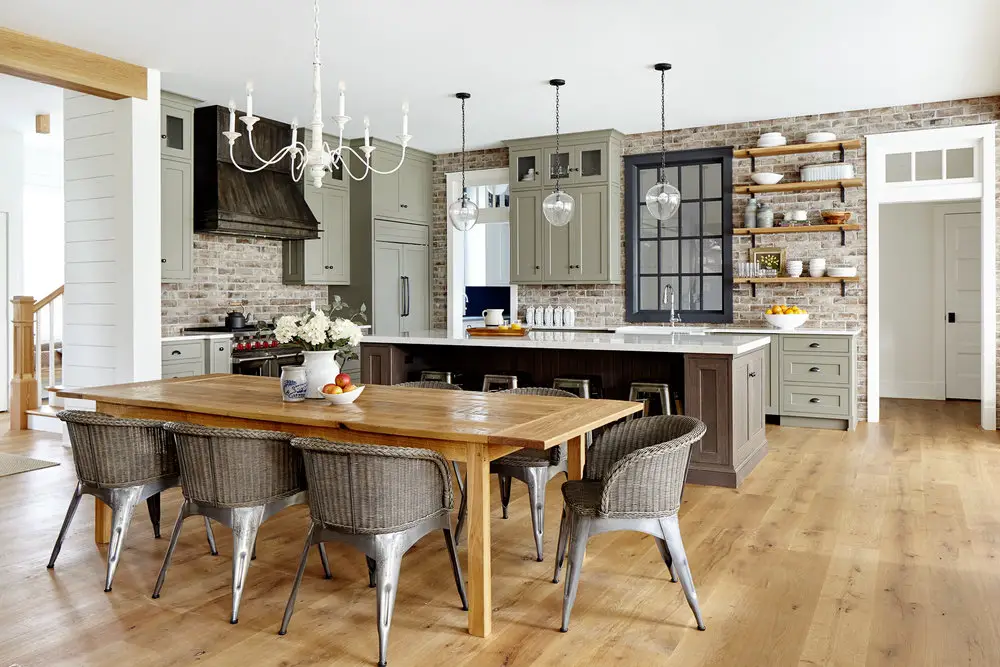
Shotcrete is an efficient way to pour concrete in difficult areas for the concrete to reach; it is durable and best for mine shafts and tunnels. The better the ingredients you have, the better you will get the durability. You can also connect at http://www.proshotcretebrisbane.com/ for any expert help.
Thanks to proshotcretebrisbane.com for consulting on this post.
Leave a Reply